Inspection for reverse engineering
When reverse engineering an existing component or assembly it is critical to understand your starting point. Basing a design on a single example risks that sample being a poor representation of the original design. Where possible, a sample of parts should be measured and inspected to ensure that the resultant nominal part is as close to the original design as possible. For these activities, Physical Digital conducts trend analysis to either identify the part most representative of the given sample or create a ‘Golden Mesh’ which is a combination of the full sample filtered and averaged to best represent the part as originally designed. With a part identified, full geometric inspection is carried out to provide a comprehensive set of dimensions from which a new design-intent model can be created. We use our wealth of experience in design for manufacture and design for assembly to determine the difference between deviation from design through manufacture or use and design intent providing functional models for use in the future.
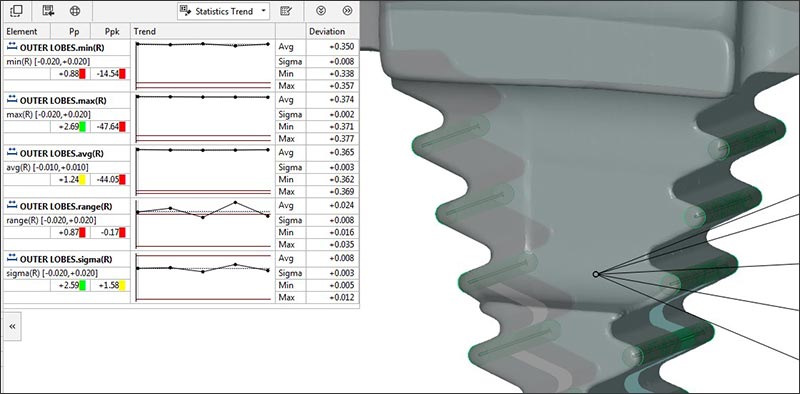